7 Lean Methodology Benefits for Development Teams
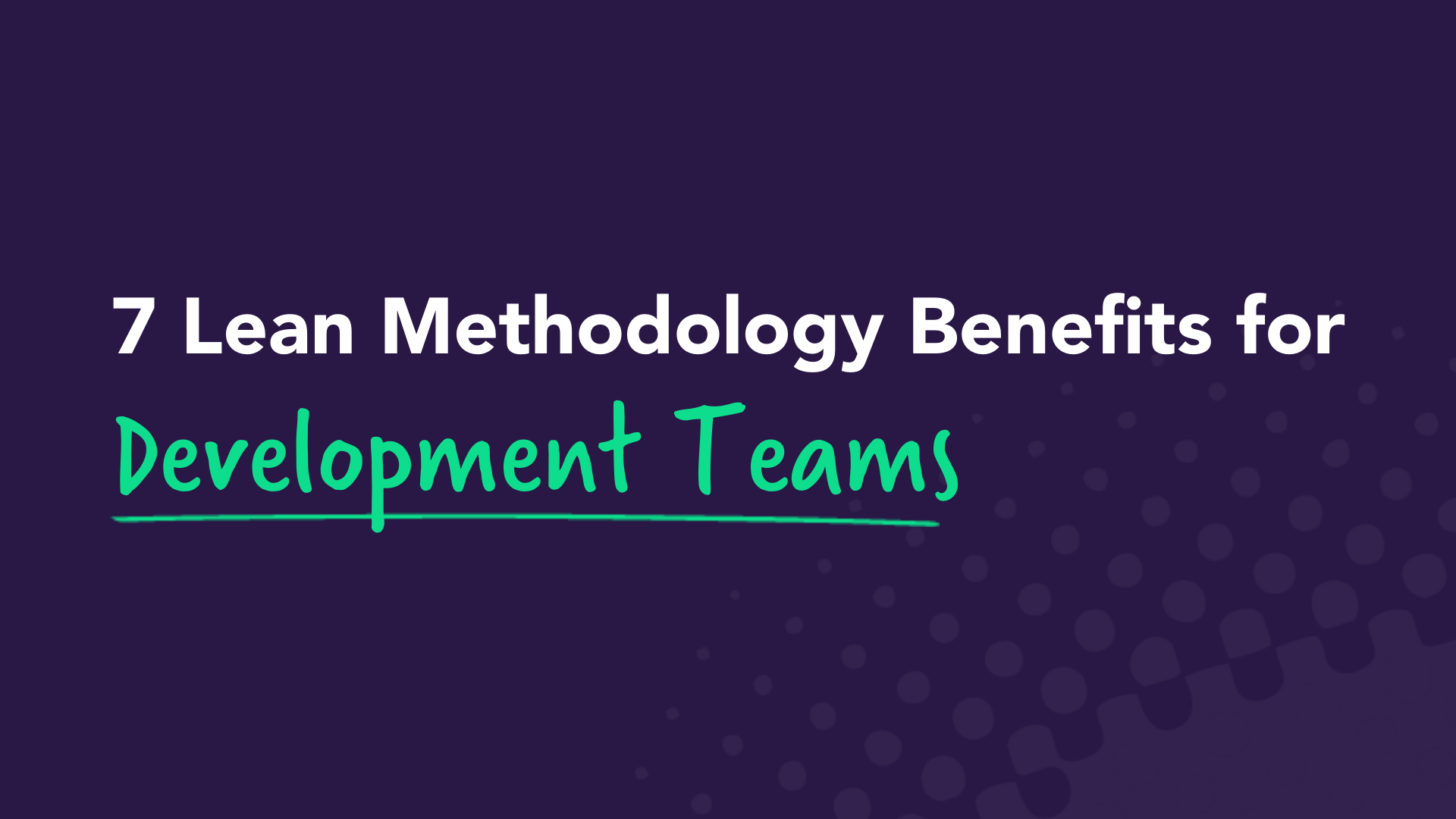
The lean methodology is all about eliminating waste and improving efficiency to maximize and deliver consistent customer value. Under lean, if a process doesn’t bring value to the customer, it’s considered wasteful and is eliminated or reduced as much as possible. It’s a development method and guiding mindset that helps teams refine their processes in the name of efficiency, effectiveness, and continuous improvement.
Here, you’ll learn about the origins of lean as well as 7 key benefits of adopting the lean methodology.
An intro to lean methodology
The lean methodology grew out of lean manufacturing. The concept was introduced in manufacturing to improve profits by reducing costs as opposed to relying solely on increased sales. If a company can eliminate waste and become more efficient, it can save money, which increases overall profits.
While the roots of lean manufacturing can be traced back to the 1400s, Henry Ford first fully integrated the entire production process, creating something called flow production in the form of an assembly line.
This was a revolutionary change in car manufacturing, but while Ford certainly enhanced flow, he didn’t leave much room for variety. In the 1930s and ‘40s, Japanese manufacturers Kiichiro Toyoda, Taiichi Ohno, and others at Toyota made a series of simple innovations that allowed them to provide both continuity in process flow and a wide variety of vehicles, creating the Toyota Production System.
This form of lean production enabled the elimination of waste, reduced costs, increased efficiency, and made information management simpler and more accurate. Lean methodology was further distilled and explored in the books The Machine That Changed the World by James P. Womack, Daniel Roos, and Daniel T. Jones, and Lean Thinking by James P. Womack and Daniel T. Jones.
The latter book also introduced the five key principles of lean:
- Identify Value
- Map the Value Stream
- Create Flow
- Establish a Pull System
- Seek Perfection
Learn more in our article, Understanding Lean Agile and the 5 Lean Principles.
Of course, lean thinking has evolved beyond manufacturing and has been adapted and applied to everything from healthcare to construction to logistics and distribution to government to software development.
1. Increased efficiency ⏳
The application of lean to business processes is all about reducing waste to increase efficiency. But how do you figure out which processes provide value?
Once customer value is identified, teams can create a value stream map. Value stream mapping tracks each of the steps and processes to bring a product from inception to delivery. Organizing your processes visually where everyone can see them allows teams to clearly see what does and doesn’t provide value. If any steps or processes don’t bring value to the customer or are found to be otherwise wasteful, they are eliminated or reduced as much as possible.
A team can’t be efficient if they’re wasting time on tired processes that don’t provide customer value. Adopting lean methods helps to get rid of those processes, so you can dedicate your team’s energy exclusively to the processes that do, thereby increasing your team’s value flow, efficiency, and productivity.
2. Reduced bottlenecks 🛑
A bottleneck or broken process, no matter how small, can totally derail a workflow or make it impossible to meet a deadline.
With lean, tasks aren’t blindly or randomly assigned. Teams work together to ensure work is evenly distributed and deadlines are met. They discuss any potential bottlenecks in advance so they can be solved before they become a financial burden or delay work. Since capacity and WIP (work in progress) items are continually forecasted, monitored, and adjusted with lean, bottlenecks are anticipated in advance, every team member participates, and no one’s time is wasted.
3. Fewer costs (and fewer surprises!) 💸
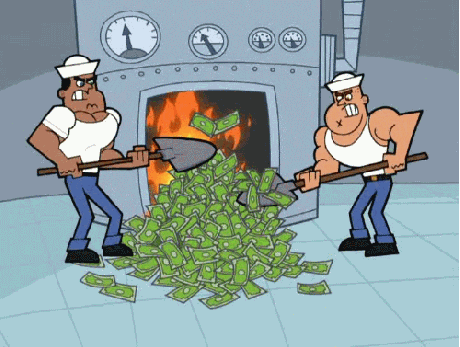
Eliminating waste means saving money—no matter the industry. Overproduction, having too many materials to store, overhiring, and production bottlenecks are expensive and wasteful. These wastes can be eliminated with better management of processes and systems, enabling companies to always have the right number of employees, amount of materials, and working hours at any given time.
Adopting the lean methodology means increasing efficiency, which benefits any company’s bottom line. Make sure every cost is accounted for and necessary to the production process by consistently reviewing your company’s work processes and eliminating any costs that don’t add value.
4. Systems can adapt better and faster 🌎
Businesses today must adapt faster than ever due to increasing customer demand, rapidly evolving technological advancements, and the COVID-19 pandemic.
The larger the size of the organization, the harder it is to adapt. Long-running business systems were not designed to be flexible, so when adjustments need to be made, it may take months or years before the entire organization is on the same page.
With lean, teams can better adapt. Lean systems aren’t as rigid, so it’s easier to make adjustments along the way, meaning teams will better adjust for unexpected circumstances. The lean methodology can help any business, no matter its size, adapt to changing times gracefully, as lean is the exact opposite of a set it and forget it process.
5. Stakeholder visibility and strong customer relationships 💞
The lean methodology leans into both stakeholder and customer needs, which results in a better end product. Progress in lean is measured based on the value delivered to the customer instead of the completion of tasks.
With lean, customer value is paramount. Every project and task begins with considering the point of view of customers and putting yourself in their shoes. Feedback is gathered alongside product development instead of at the end to ensure new information is considered and that the final product will be exactly what the customer needs or wants.
6. Continuous improvement mindset 🧠
Lean is the enemy of the status quo. Lean demands the constant fine-tuning and refinement of processes and enables a continuous improvement mindset. It’s not a “set it and forget it” process, as lean is all about consistent process improvement. No matter how successful or efficient the company is, there is always room for improvement and new, innovative ways to bring value to the customer.
This attitude instills a continuous improvement mindset in everyone involved on the team, whether it’s a small development team or an entire lean enterprise (SAFe). Teams can anticipate and expect regular feedback from leaders, managers, and stakeholders. With lean, innovations and iterations are less precious and more plentiful. The team continues to improve and fine-tune their skills and processes with each passing product.
7. Increased team engagement 🤝
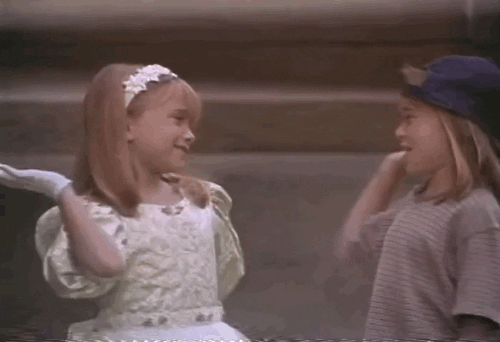
Employee disengagement is expensive. Disengaged employees have higher absenteeism, lower productivity, and lower profitability — all of which can majorly drain a company’s resources. If a company’s culture doesn’t inspire employees to show up and do their best, that company is going to hemorrhage money every year until its bottom line bottoms out.
A lean organization, on the other hand, puts teams on the frontline of product development. Under lean management, employees have direct and regular contact with managers about how their work is going and how the process could be improved. Since teams are more involved in the process, they are more engaged and more likely to actively participate, provide feedback, and buy into their work.
Engaged employees are a company’s greatest asset. Bringing everyone into the process gives teams ownership over the outcomes, boosting their creativity as well as their accountability. Increased team engagement means enhanced efficiency, effectiveness, and team morale.
You can apply the lean methodology anywhere to reduce waste and improve efficiency. Let’s recap. The top benefits of adopting lean include:
1. Increased efficiency
2. Reduced bottlenecks
3. Fewer costs (and fewer surprises!)
4. Better and faster systemic adaptation
5. Stakeholder visibility and strong customer relationships
6. Continuous improvement mindset
7. Increased team engagement
Agile made easy
Easy Agile can help your agile team work better together to deliver for your customers. We have a suite of agile apps for Jira designed to put the customer first through every step of the product development process. From team agility with Easy Agile TeamRhythm, to scaled agility with Easy Agile Programs, our plugins work with multiple agile frameworks, including Kanban and Scrum.
If you work with Jira, you’ll find our lean tools especially helpful for improving the functionality of your workflows and enhancing team collaboration.
Related Articles
- Workflow
Understanding Lean Agile and the 5 Lean Principles
Waste is expensive! 💸 It’s paying someone not do any real work, paying for supplies you don’t need, or paying for team members to sort out a preventable issue. Lean agile aims to eliminate wasteful resources and tasks for improved efficiency and reduced costs — while never sacrificing quality. In fact, lean agile prioritizes bringing value to the customer with every decision that’s made.
Lean agile is a development method that helps teams identify waste and refine processes. It’s a guiding mindset that facilitates efficiency, effectiveness, and continuous improvement.
Consider this: You probably work a lot better when your desk isn’t completely covered with a mess of things you don’t need. When you eliminate distractions and waste, it establishes an organized workspace and workflow. This helps you focus on what’s most important, ensuring you work efficiently and effectively.
Here, you’ll learn more about the development of lean, the benefits of lean agile, and the five core principles of lean.
The development of lean agile
Lean agile, or lean software development, originates from the principles of lean manufacturing. The concept was brought into manufacturing to improve profits by reducing costs instead of solely relying on increased sales. If a company can eliminate waste and become more efficient, it can save money, thereby increasing overall profits.
Lean agile is an agile methodology that, in basic terms, is quite simple: improve efficiency by eliminating waste. Unlike traditional, waterfall project management, which dictates a set plan laid out by a project manager, lean agile strives to reduce all tasks and activities that don’t provide real value. This helps ensure everyone involved in a project or product development can work at optimal efficiency.
If you’re looking to dive into the history of lean agile, Lean Enterprise Institute Inc., founded in 1997 by James P. Womack, PhD, is a leading resource for lean methodology. It aims to help people and teams work better through lean thinking and practices.
Lean practices are popular because they can be applied to other agile approaches and software development methods. Lean agile provides a clear application for scaling agile, which is often difficult for large or growing organizations.
The benefits of lean agile
In case you’re not on board with lean agile yet, let’s review its main benefits.
Waste less time
Time is wasted when processes don’t run smoothly. In lean manufacturing, it’s important for goods and services to be delivered quickly and effectively. No one's time should be wasted on the job, and companies should aim for shorter lead times without sacrificing quality.
Wasting time in any industry is expensive, but it’s particularly important to pay attention when working in agile software development. Even a small bottleneck or broken process can completely throw off a workflow or product deadline. Lean agile helps development teams manage time effectively to ensure everyone is utilized, no one's time is wasted, and roadblocks are anticipated in advance.
Reduce costs
When businesses eliminate waste, they save money. In its original form, lean manufacturing ensured companies had the right amount of materials, employees, and working hours at any given time. Overproduction, overhiring, or simply having too many materials to store are expensive wastes that can be eliminated through better management of systems and processes.
Any business, no matter the industry, will save money with improved efficiency. Lean agile ensures that waste is continually eliminated and agile teams continue to fine-tune processes for optimal efficiency.
Improve work quality
With lean agile, it’s not only about efficiency — it's about maintaining efficient processes while bringing a quality product to customers and stakeholders. When businesses intentionally improve processes, they remain competitive. Lean principles consider the customer value of any action or decision to ensure needs are always met or exceeded.
The five principles of lean agile
There are five core principles for implementing lean methodology:
- Value
- Value stream
- Flow
- Pull
- Perfection
These principles describe a five-step process that guides the implementation of lean techniques for manufacturing, software development teams, and other agile practicing industries.
1. Identify value
The first step requires you to step into the shoes of the customer. Value is what the customer needs and wants from a specific project or product.
Consider from the customers’ point of view: What are their expectations? What are they willing to pay for? How do they want their needs met?
Sometimes, customers may be unable to define exactly what they’re looking for — especially if it’s a new product or technology they’re unfamiliar with.
In any case, the project cannot move forward without clearly identifying what it will take to provide customer satisfaction. You’ll need to identify the end goal (value) customers are hoping to find with the product or service.
2. Map the value stream
Next, the team visually maps each of the steps and processes it will take to bring the product from inception to delivery. By making each step visible and always keeping the value top-of-mind, it’s easier to see which steps don’t directly contribute to continuous delivery. Once wasteful steps are found, the team finds ways to eliminate those steps or reduce them as much as possible.
Getting rid of waste ensures your company doesn’t unnecessarily spend money on steps and processes that don’t add value. And — most importantly — the customer gets exactly what they’re looking for.
3. Create flow
Once the waste is eliminated from the value stream, the next step is ensuring the remaining processes work as effectively and efficiently as possible, which means no delays, disruptions, or bottlenecks. It’s important for the steps that create value to work in tight sequences to ensure the product flows smoothly toward the customer.
In order to achieve this kind of agile transformation, lean businesses must train their employees to be adaptive and multi-skilled, create cross-functional teams, break down and reconfigure steps in the production, and balance employee workloads.
4. Establish a pull system
With enhanced flow, your team can deliver products and services faster. A pull system enables “just-in-time” manufacturing and delivery, limiting inventory and work in progress (WIP) items by only producing enough to meet customer demand.
By establishing a pull system, you create products and services as needed as opposed to creating them in advance, which leads to a growing inventory or list of tasks that need to be stored and managed — draining your bottom line.
5. Seek perfection
By completing steps 1-4, waste is eliminated — for now. However, the work is never done. There is always a process that could be improved, and there will always be steps in project and product development that waste time and money or don’t deliver value. That’s why the fifth step of seeking perfection is key.
Lean takes time to implement, and going through the process once is not enough. Build a continuous improvement mindset into your company culture, and never settle for the same old.
Lean agile made easy
Lean prioritizes the elimination of waste to improve efficiency. This helps teams continually improve their processes while emphasizing the tasks that bring the most value to customers.
If you’re looking to learn about how agile principles work with other development approaches, we recently covered eight different software development methodologies, including rapid application development, extreme programming (XP), and other agile frameworks.
Easy Agile is dedicated to helping teams improve their processes and agile methods. Our Jira plugins help product owners, Scrum Masters, and development teams align around product goals, workflows, and customer needs. The tools are simple to use, collaborative, flexible, and they work seamlessly with Scrum, Kanban boards, and other agile processes managed in Jira software.
You can contact our team or watch a demo to learn more about our tools and follow our blog for the latest content on Jira, agile, lean, and the development process.
- Workflow
How Lean Principles Support Productivity and Performance
Lean principles focus on delivering greater customer value by using minimal resources. Enterprises use these lean principles to practice continuous improvement based. They base their improvements partly on the practice of zero waste.
Here, you can improve your knowledge about lean principles to increase productivity. You can also use software tools to support positive change in your work environment. A lean-agile team is more productive and team members get to share their new knowledge.
The history of lean principles
Inspired by Ford’s mass manufacturing system, Eiji Toyoda created the "Toyota Production System.” This served their customers and introduced "Just-in-Time" (JIT) manufacturing.
JIT means only stocking enough vehicles to streamline rapid production. By only keeping an inventory of required parts on hand, a company saves money and time.
Starting here, the lean methodology has evolved over time. Now, lean consists of three main concepts of purpose, people, and processes.
The purpose of lean concepts is to give the customer what they want, reduce waste, and focus on employee morale. It also encourages accountability. Lean promotes ownership of work, problems, and successes.
Overview of lean principles
Organizations use lean principles to enhance overall performance. They do this by being careful how they use their scarce resources to meet customer demand.
The concept and practice of lean principles include:
- Elimination of waste
- Incorporating quality via end customer value
- Generating knowledge among team members
- Postponing workflow commitments
- Produce rapid delivery
- Respecting people
- Encouraging holistic process improvements
Practicing the lean principles
The lean principles require lean processes and lean tools. Therefore, if you want a lean organization, the leadership must support lean thinking and provide employees (people) with the tools to achieve this aim.
Here’s how to enact the lean principles:
Focus on value
This means producing products that customers want by encouraging them to provide details and feedback about products and services.
Kaizen is a part of Japanese philosophy that highlights the elimination of waste in a quest to change for the better, thus producing greater customer value.
Use value stream mapping
This process involves mapping out all the people and the actions needed to deliver a desirable end product. You get to see which processes work and which do not add value. You also have a better chance of identifying bottlenecks before they become a problem.
Once you do a bottleneck analysis, you can eliminate obstacles and improve processes. A bottleneck analysis involves getting to the root cause of what is holding up completion of the work and finding better processes to align all work batches that are dependent on each other.
Develop a logical workflow
To do this, you’ll focus on implementing the correct steps to create value in a logical sequence.
You can help streamline workflows by using Scrum sprint principles and break the work into smaller parts. You can also use tools like strategic roadmaps to visualize and improve Scrum or Kanban workflows.
Develop a pull system
A pull system ensures that teams know what to do and when, so they use less effort in creating outputs.
A pull system responds to demand. If there is a demand for a product, you respond by doing whatever is necessary to meet that demand. Knowing there is demand helps reduce non-value processes and optimize resources by using JIT or Kanban.
Encourage continuous improvement
You can use the Kaizen approach and other elements of the lean philosophy to enhance continuous improvement by constantly finding ways to do things better.
One way to do things better is to continue checking your value stream mapping to ensure that everyone stays on board. You must also ensure that all employees participate in lean processes and actively look for ways to improve the supply chain.
The benefits of implementing lean processes
Any organization that wants to take the lean principles route can anticipate some excellent benefits.
Several of these benefits include:
- Improving team member and team communications
- Empowering people to make decisions and engage in ongoing positive change
- Developing integrated cross-functional teams who share knowledge and skills
- Enhancing end goal delivery to augment end customer value
- Reducing the overall time to deliver that value to customers
Besides using Scrum stand-up meetings and software development tools and processes, you can use more lean tools to create a team or organization that embraces lean thinking.
Lean principles tools
Organizations can use metrics such as sales data and customer feedback as tools to assess customer demand. But, only after identifying the value can organizations use the lean tool of value stream mapping to further their end goal.
You can also browse through the information resources at the Lean Enterprise Institute to learn more about lean principles. You can also explore other lean thinking such as Six Sigma, Error Proofing, Plan-Do-Check-Act (PDCA), and other tools to support a lean organization.
Jira software tools from Easy Agile
Easy Agile provides organizations and teams with multiple tools to help streamline their workflows. For instance, you can use Jira to help develop logical workflows and get your teams up to speed on lean thinking.
Tools like Easy Agile Scrum Workflow for Jira are available at no cost to ease this positive change. Another tool that complements value stream mapping is Easy Agile Programs for Jira.
Adopting lean principles is much easier with the support of Easy Agile resources, so get your lean team going today.
- Agile Best Practice
Being Agile vs Doing Agile
Being agile vs doing agile – what’s the difference?
Organizations around the world have recognized the need to respond rapidly to meet the challenges of constant change. As a result, they’re racing to adopt agile ways of working, with the pandemic accelerating agile adoption.
Those who get it right can make a powerful impact on their bottom line and their competitive edge. But for others, the benefits may yet to be seen.
This is where ‘doing agile’ versus ‘being agile’ can make all the difference. Because to truly reap the benefits of agile methodology, organizations need to shift from doing to being.
This article will explain the difference between being agile vs doing agile. Plus, we’ll take you through some of the common challenges many organizations face in their agile journey.
Key points
- To realize the full potential of agile ways of working, teams must cultivate an agile mindset as well as adopt agile processes.
- Moving from ‘doing agile’ to ‘being agile’ takes time, coaching, and a new approach to management.
- Done right, being agile can amplify customer satisfaction, employee engagement, growth, and profitability.
Why agile, and why now?
Agile had already been rising in popularity for over 20 years, but once the pandemic hit, this growth accelerated.
Across every industry, being able to deliver digital experiences is now crucial. Organizations now need to act and think like software companies, with a laser focus on the customer’s online experience. Together with an active approach to finding customers, you need to deliver real value to stand out from competitors.
For organizations looking to survive - and thrive - in this environment, many are turning to agile frameworks to rapidly add customer value and drive business results. Being agile allows teams to:
- Make the complex simple – by working within a clear, structured framework, chaos turns to order.
- Maintain a clear overview – agile teams have a shared understanding of their progress towards their goals.
- Replicate success – if a team finds an effective way to deliver results, they can repurpose and share solutions across the organization.
- Create an aligned, purposeful culture – when hundreds of people across one organization form dozens of agile teams, they build a stable backbone, walking the same path towards the same goal.
"Agile organizations, viewed as living systems, have evolved to thrive in an unpredictable, rapidly changing environment. These organizations are both stable and dynamic. They focus on customers, fluidly adapt to environmental changes, and are open, inclusive, and nonhierarchical; they evolve continually and embrace uncertainty and ambiguity. Such organizations, we believe, are far better equiped than traditional ones for future."
What does it mean to be agile?
Many organizations incorporate a few agile processes to manage projects. But that doesn’t mean teams have fully understood and embraced the agile methodology. It could be that they’re ‘doing agile’ rather than actually ‘being agile’.
Here’s the difference between the two:
Doing agile
‘Doing agile’ is the misconception that if you do agile things your company will become agile and responsive to change. Organizations that have fallen into this trap may go through the motions of some agile processes, such as daily stand-ups, sprints, and retrospectives. Teams are structured to be small, cross-functional, and collaborative. But by stopping there, those teams don’t become truly agile and they may struggle to see results.
While agile ceremonies, tools, and structures are critical in implementation, they are only part of what makes an organization agile.
Being agile
‘Being agile’ means you incorporate the above activities but go beyond the processes. This means applying an agile mindset and agile values to all areas of the organization. Teams will need training to master the agile mindset and push through any challenges along the way. It takes more time and effort than simply doing agile, but it’s critical if you want to reap the benefits.
What’s an agile mindset?
Embracing an agile mindset means understanding and living its four core values. To be agile, you need to:
- Respect people - Recognize that people are critical to the success of your organization. Ensure people share common goals, feel safe and empowered to share ideas, and adopt a ‘we’ versus ‘I’ mentality.
- Optimize flow - Build in quality at each increment so you can identify issues and course-correct early. This helps maximize value and minimize waste while creating a consistent, sustainable flow of work.
- Encourage innovation - Foster experimentation with collaboration, constructive feedback, and autonomy. Schedule time and space for creativity and ideas to flow.
- Relentlessly improve - Keep in mind that there is no endpoint with the agile mindset. It’s about continuous improvement, so you need to continually reflect and improve future processes as part of an ongoing practice.
To take these values and make them the foundation of working across your organization, you need to combine agile processes with an agile mindset. Without the agile mindset, you’re not ‘being agile’, and your processes won’t deliver your organization’s full potential.
"The agile mindset is a thought process that involves undersatdning, collaborating, learning, and staying flexible to achieve high-performing results. By combining the agile mindset with processes and tools, team can adapt to change and deliver incremental value to their customers."
Agile processes and tools aren’t enough
Agile processes, including the ceremonies, tools, and apps, are there to support the mindset of the team. But without getting the mindset right across your organization, you won’t be truly agile.
Fostering the agile mindset gives an organization the ability to rapidly move in any given direction at any given time to deliver the best value to customers. Teams who’ve mastered agile are usually:
- Autonomous and empowered to make decisions around the product and customer experience.
- Able to adapt to change quickly.
- Always willing to learn something new.
Engaged with a shared purpose and collaborative culture.
"It's about being able to pivot to change. Whether that's in terms of people, or resources or budget - whatever that looks like for an organization. If you're able to quickly shift from one area of focus to another before your competitor does, then you have a competitive advantage in the market."
- Sean Blake, Head of Marketing, Easy Agile
Common challenges to look out for as you move from doing agile to being agile
The sooner you can act and move from doing agile towards being agile, the sooner your customers, employees, and your bottom line will benefit.
Here are a few common challenges and tips to overcome them.
- People might hold onto old habits
People find change hard, especially when habits are ingrained. You might find some people dig their heels in, clinging to the old way of doing things. It’s important to remember it can take time, and people will need support to learn new ways of working. Be sure to bring in plenty of opportunities for feedback and discussion so you can reiterate as a team to find a process that works for your organization. - It’s not just the team who needs to be coached
Being agile is a mindset for the entire organization, including managers and executives. If your leaders don’t understand and support agile, it will be hard to get traction and shift old processes and hierarchies. Scrum Masters and Agile Coaches need to spend time coaching leaders to develop new agile mindsets and capabilities. - For many organizations, being agile requires a new style of management
The traditional command-and-control management style may have worked in the industrial age. But now it’s a mismatch for the way organizations and people need to work today, and it doesn’t support the agile mindset. To be agile, teams need the trust, autonomy, and ability to take an idea through to execution without any roadblocks. Senior executives must get behind this multifaceted cultural-transformation effort for this to happen.
Are you ready to be agile?
Moving beyond agile processes to scale an agile mindset across an organization isn’t something you can tackle overnight. It takes time, effort, training, and leadership support to internalize agile values and move beyond the command mindset of the past.
You may face challenges along the way, you’ll discover there’s always more to learn, and you must be agile in your adoption of agile.
But the prize for true agility is significant, including increasing customer satisfaction, boosting employee engagement, and improving productivity - making it well worth the investment.
Agility helps modern organizations thrive through change in an uncertain and unpredictable world. For most of us, it’s no longer a desirable way of working - it’s essential.