How to Complete the Value Stream Mapping Process
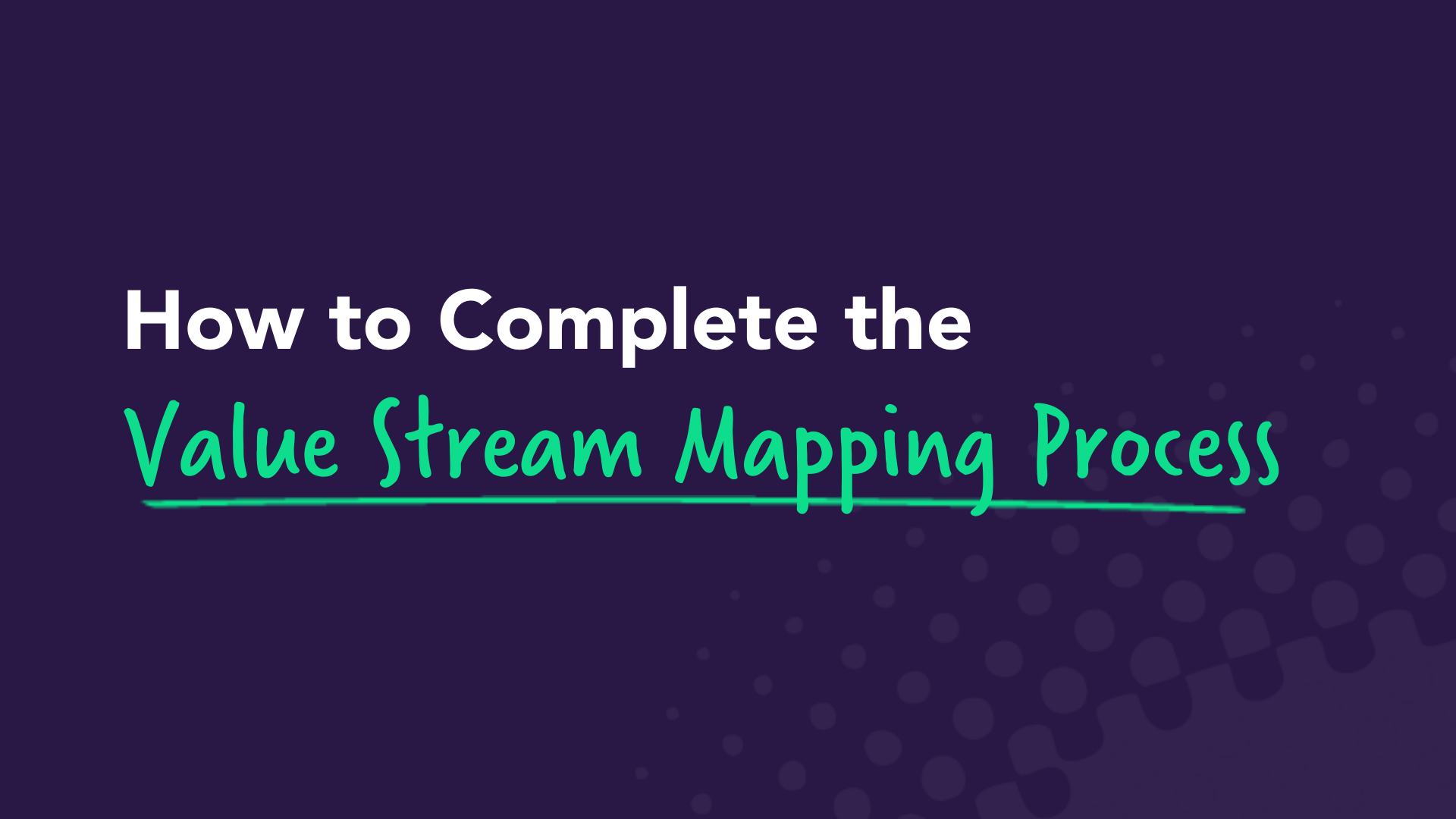
"Bottleneck" is a buzzword you don't want to hear. When it comes to your production process, maximizing your time and budget is all about keeping efficiency high. However, simply cutting the steps in your process may not make your customer any happier. If you want to achieve a high return on investment and increased customer satisfaction, value stream mapping is an ideal way to keep your team on track.
What is value stream mapping?
Value stream mapping (VSM) is a technique from the lean principles methodology that helps you visualize the steps you need to take to deliver a finished product or service. Value stream maps outline the flow of information and the physical materials to see where value is added for the customer. The purpose of VSM is to increase efficiency by reducing waste in the production process.
Widely known as the lean manufacturing method used in the Toyota Production System, VSM is now often used to eliminate bottlenecks in other industries like software development, supply chain, and healthcare. It's a versatile technique that can help many organizations shine. 🌟
Streamline visibility and provide transparency of your Program for all teams
Easy Agile Programs
Why value stream mapping matters
When companies aim for efficiency, they often focus on reducing the total amount of production steps required. But customers don't always see what happens behind the scenes. Decreasing the length of your workflows mainly benefits your process without changing the experience for them. On the flip side, the value stream mapping process keeps your team members aware of customer needs, so your business can stand out.
For teams that use value stream mapping, reducing inefficiencies is all about cutting production process steps that don't add value. Value stream maps are a visualization of where you're wasting effort. They show your team that keeping steps within your process is okay — but each of those steps should help customers in some way. As a result, VSM prevents overproduction while ensuring your customers are happy with your final product or service.
You can achieve better lean agile workflows with value stream mapping and effectively keep up with customer demand. 💪
Value stream mapping terms
A typical value stream map is divided into three key sections — information flow, material flow, and lead time ladder — that help you see where process improvements can occur. To help you complete each part of a value stream map with greater ease, we'll explain a handful of common terms that you'll come across in each section.
As you learn these terms, you can refer to this Microsoft template to see a few VSM symbols that you'll often use.
Information flow
At the top of a standard value stream map is an information flow section that shows how data transmits between your team members, customers, and other stakeholders. Common terms you'll need to know to complete this section include:
- Customer: This is the consumer who will receive your final product. Your customer is represented in the upper right corner of your map.
- Supplier: This is your organization. Suppliers are placed in the upper left side of value stream maps.
- Dedicated process flow: This is a process or department (like "production control") that information flows through.
Material flow
In the middle of a value stream map is a material flow section that shows how you take your product or service to delivery, step by step. Each box represents a unique task, which may be performed by the same team or by another after a material handoff.
To complete the material flow section, you need to know these terms:
- Shipments: On value stream maps, "shipment" arrows point from the supplier to the first step in the material flow, or from the last step to the customer. They show how your information flow is related to the start and end of your production process. For example, an arrow can show how raw materials move between the supplier and factory or how software access is "sent" to a user.
- Cycle time (C/T): This metric represents the amount of time required between shipments.
- Inventory: Inventory is what's produced between each stage of the production process. Your inventory is usually written below a triangle with a "I" within it. 🔺
Lead time ladder
At the bottom of a value stream map is usually a time ladder that helps you visualize your lead time, which is the average time spent on each step of your material flow.
Kaizen burst
Throughout your value stream map, you can include Kaizen bursts. These represent bursts of activity (like a sprint) in which your team focuses on resolving a specific issue — such as processing customer returns — to quickly remove potential bottlenecks. The symbols for Kaizen bursts look like comic book explosions to grab your attention. 💥
How to create a value stream map
When you're ready to get started with value stream mapping, select the specific product or service that you want to create a map for. While all production processes can benefit from continuous improvement, you should ideally start with a product or service that could benefit the most from VSM. Once you've made your selection, follow these steps with your VSM team:
- Define your objective: Identify what you want to change for the customer as a result of the value stream mapping process. For example, you might want to improve the quality of a product or the speed with which you deliver a service.
- Clarify your scope: Define the start and end of your value stream map. You can create a map that includes all of the steps between concept and delivery, begin with an inefficient part of your value stream, or end with a contract agreement instead of a traditional delivery.
- Outline your process: List each step of your production process. Begin by speaking with team members from each department involved in the process to gather any needed insights. Your list should include non-value producing steps. Collect data about cycle times, lead times, inventory, and more to understand each step even further.
- Create and evaluate your current state map: Using the information you’ve gathered, create a map that reflects the current state of your process. Work with your team to identify which steps are productive and where improvements are needed. This map will allow you to pinpoint areas of waste, like long process times or software downtime.
- Develop a future state value stream map: Create a second map that illustrates an improved process that eliminates non-valuable steps. This will be the map you'll ultimately follow to reach your objectives.
- Build an implementation plan: To start moving toward your future state, establish how your team will implement the new process. Include what metrics you'll keep an eye on to ensure you're on track to reach your objectives. You can also establish how frequently you'll review your progress and adjust your future state map (if needed) during the implementation phase.
📣 Achieve team alignment at scale with Easy Agile Programs
Continue adding value for your customers
Learning to see from your customer's perspective is crucial to ensuring you stand out from your competitors. Following the value stream mapping process can help you visualize where your team is producing value and where you're doing extra work that can easily be eliminated.
To continue adding value for customers, learn how Easy Agile Programs can help you dive deeper into your product’s customer's journey.
Related Articles
- Jira
Streamline Your Sprints With 9 Jira Automations
Sprints are at the core of agile principles. And they’re how a Scrum team uses a predefined time period to work together towards an agreed-upon goal. A sprint focuses on interaction and collaboration to produce working software. A team has to do a lot of work to maintain their sprint workflows in Jira. Changing task statuses, notifying teammates to sprint changes, and keeping developers’ code changes in sync with Jira tasks can all add up to a lot of manual mouse clicks. 🖱
Many of these manual steps can be automated to save your team effort.
Help your Scrum team with Jira automations
Scrum is a framework for getting agile work done. The Scrum events are:
- Sprint: The time period in which the team works toward their sprint goal (e.g., completing a set amount of user stories from the product backlog). The next sprint starts when the previous one ends.
- Sprint Planning Meeting: A meeting that scopes the amount of effort required for backlog items prioritized by the product owner. The software development team commits to completing that amount of work.
- Daily Scrum: A brief meeting each workday when Scrum team members update each other on the progress of their work within the sprint. It's a time to lend support or unblock another team member who may be stuck on an issue.
- Sprint Review: A time for the Scrum team and stakeholders to review the outcomes of the completed sprint and discuss what impacts they have on future sprints.
- Sprint Retrospective: A meeting to find opportunities to improve on the team's agile processes and its interactions with each other.
Which Scrum roles are involved:
- Software Developers: They get the work done but don't want any sprint surprises.
- Product Owner: This person prioritizes the work and sometimes has to make unplanned mid-sprint changes.
Every player on the software development team, from startups to established companies, has repetitive tasks they need to perform throughout its sprint events. Because we're all human, when we're sprinting, we sometimes forget to transition the status of issues or do the little things in Jira that keep everyone on the team aware of what's happening in our sprint in real-time.
Automate your sprint workflows with Jira
Have no fear. Jira can help automate typical sprint workflows like task transitions and team notifications. 🤯 Agile project management within software development is a methodology that is conducive to automation. You can link behaviors in your Jira issues to trigger actions from tools like Slack and MS Teams, email, GitHub, Bitbucket, and GitLab.
You can use Jira automations to do things such as:
- Notify team members and stakeholders of any changes to a sprint
- Trigger actions based on task transitions within a sprint iteration
- Keep Jira task and sub-task statuses and story points in sync
- Connect code commits and build statues to Jira issues
Oh my!
If you didn't know these tools existed, here's your chance to learn them.
Automate your way to connectivity
Keep agile teammates in the know
When a sprint begins, it's important the product owner notifies team members if something changes. That way, you can make sure it won't negatively impact your ability to complete your sprint goal.
Communication within agile teams is paramount, and Jira provides ways to automatically notify your scrum team based on rules you set about your sprint. For example, you can send emails or Slack notifications when the status of a task changes.
Task and sub-task coordination
Sub-tasks are a handy feature in Jira. They help you break tasks into smaller steps and track their progress as they're being worked on. Scrum masters encourage this universally in agile, but it can be easy for sub-tasks to get out of sync with their parent tasks. We’ll soon learn a Jira automation to prevent this.
Connect developer code work to Jira issues
Your development team has a lot on its plate during a sprint. Not only does it have to complete all of its user stories — but there's also the mechanics of keeping code commits by developers synced with their associated Jira tickets. And, always remembering to keep these in tune with Jira tickets is burdensome. As you’ll see, there are ways to connect actions taken in GitHub, Bitbucket, and GitLab and update Jira tickets.
Jira automations FTW
Here are our nine favorite Jira automations that streamline our sprint workflow.
1. Notify teammates when a story is added to a sprint
Scope creep (adding new points to a sprint after it starts) is nobody's friend. However, there are times when a product owner needs to pull an item from the product backlog and add it to the current sprint. When this happens, it's best practice to inform the whole team that a change has been made. Use this handy automation template to send an email to your team when backlog items are added to a sprint.
2. Automatically assign a task when its status changes
Some team members need to be made aware when an issue transitions to being on their plate. When an issue’s status switches to In Review, for example, you can auto-assign it to a QA teammate.
3. Celebrate when your sprint is over by sending a Slack message
A lot of work happens during a sprint. Because your next sprint always begins immediately when the current one ends, it's often difficult to find time to celebrate wins. Use this celebration to send a fun Slack message to your team when the final issue in the sprint is completed. You can make sprints fun with automation!
4. Automatically put In Progress issues into the current sprint
There are lots of moving parts when trying to ensure that In Progress Jira issues are visible in the current sprint. Nobody wants hidden work. When a developer moves a task into In Progress, you can automatically assign it to the current sprint.
5. Sum the story points of sub-tasks and update the value of the parent task
Be sure that your story point totals are accurate by automatically summing the points of your sub-tasks and updating the parent task with the value. They'll never be out of sync with each other with this nifty automation rule.
6. Close an issue when all of its sub-tasks are complete
Some people like to work with sub-tasks, which is great. But it's easy to overlook closing a parent task after you've finished your work and closed all of its sub-tasks. Well … you can automatically close a parent task when all of its sub-tasks are complete so this doesn't happen. 🤖
7. Move a task to In Progress when a commit is made
Save your developers time by cutting down on redundant tasks. When a code commit is made, it means a task is being worked on. Connect Jira to your commit repository (GitHub, Bitbucket, or GitLab) so that when a code commit is made, the associated Jira issue moves to In Progress.
8. Add a comment to a ticket when a pull request is made
Adding details to a Jira ticket from a pull request can be a copy-and-paste job — but it doesn't have to be. Use a trigger to add the details from the request into a Jira comment.
9. Notify the development team when a Jenkins build fails
Certain issues can't wait to be realized by the whole team on the next daily stand-up. If your Jenkins build fails, this is an awesome way to let the whole team know by Slack, MS Teams, or email ... right away.
Make agile sprints easy
Automations in Jira make a sprint team’s life easier by cutting down on the manual work needed to keep the mechanics of a sprint running.
You can use modified versions of these automations with Easy Agile to make agile even easier! For example, celebrate roadmap wins by notifying your team when issues are completed in your Easy Agile Roadmaps for Jira, or sync your Jira data fields with your roadmap. There are many ways to mix-and-match rules and triggers to make Jira automations work for you.
- Workflow
How Lean Principles Support Productivity and Performance
Lean principles focus on delivering greater customer value by using minimal resources. Enterprises use these lean principles to practice continuous improvement based. They base their improvements partly on the practice of zero waste.
Here, you can improve your knowledge about lean principles to increase productivity. You can also use software tools to support positive change in your work environment. A lean-agile team is more productive and team members get to share their new knowledge.
The history of lean principles
Inspired by Ford’s mass manufacturing system, Eiji Toyoda created the "Toyota Production System.” This served their customers and introduced "Just-in-Time" (JIT) manufacturing.
JIT means only stocking enough vehicles to streamline rapid production. By only keeping an inventory of required parts on hand, a company saves money and time.
Starting here, the lean methodology has evolved over time. Now, lean consists of three main concepts of purpose, people, and processes.
The purpose of lean concepts is to give the customer what they want, reduce waste, and focus on employee morale. It also encourages accountability. Lean promotes ownership of work, problems, and successes.
Overview of lean principles
Organizations use lean principles to enhance overall performance. They do this by being careful how they use their scarce resources to meet customer demand.
The concept and practice of lean principles include:
- Elimination of waste
- Incorporating quality via end customer value
- Generating knowledge among team members
- Postponing workflow commitments
- Produce rapid delivery
- Respecting people
- Encouraging holistic process improvements
Practicing the lean principles
The lean principles require lean processes and lean tools. Therefore, if you want a lean organization, the leadership must support lean thinking and provide employees (people) with the tools to achieve this aim.
Here’s how to enact the lean principles:
Focus on value
This means producing products that customers want by encouraging them to provide details and feedback about products and services.
Kaizen is a part of Japanese philosophy that highlights the elimination of waste in a quest to change for the better, thus producing greater customer value.
Use value stream mapping
This process involves mapping out all the people and the actions needed to deliver a desirable end product. You get to see which processes work and which do not add value. You also have a better chance of identifying bottlenecks before they become a problem.
Once you do a bottleneck analysis, you can eliminate obstacles and improve processes. A bottleneck analysis involves getting to the root cause of what is holding up completion of the work and finding better processes to align all work batches that are dependent on each other.
Develop a logical workflow
To do this, you’ll focus on implementing the correct steps to create value in a logical sequence.
You can help streamline workflows by using Scrum sprint principles and break the work into smaller parts. You can also use tools like strategic roadmaps to visualize and improve Scrum or Kanban workflows.
Develop a pull system
A pull system ensures that teams know what to do and when, so they use less effort in creating outputs.
A pull system responds to demand. If there is a demand for a product, you respond by doing whatever is necessary to meet that demand. Knowing there is demand helps reduce non-value processes and optimize resources by using JIT or Kanban.
Encourage continuous improvement
You can use the Kaizen approach and other elements of the lean philosophy to enhance continuous improvement by constantly finding ways to do things better.
One way to do things better is to continue checking your value stream mapping to ensure that everyone stays on board. You must also ensure that all employees participate in lean processes and actively look for ways to improve the supply chain.
The benefits of implementing lean processes
Any organization that wants to take the lean principles route can anticipate some excellent benefits.
Several of these benefits include:
- Improving team member and team communications
- Empowering people to make decisions and engage in ongoing positive change
- Developing integrated cross-functional teams who share knowledge and skills
- Enhancing end goal delivery to augment end customer value
- Reducing the overall time to deliver that value to customers
Besides using Scrum stand-up meetings and software development tools and processes, you can use more lean tools to create a team or organization that embraces lean thinking.
Lean principles tools
Organizations can use metrics such as sales data and customer feedback as tools to assess customer demand. But, only after identifying the value can organizations use the lean tool of value stream mapping to further their end goal.
You can also browse through the information resources at the Lean Enterprise Institute to learn more about lean principles. You can also explore other lean thinking such as Six Sigma, Error Proofing, Plan-Do-Check-Act (PDCA), and other tools to support a lean organization.
Jira software tools from Easy Agile
Easy Agile provides organizations and teams with multiple tools to help streamline their workflows. For instance, you can use Jira to help develop logical workflows and get your teams up to speed on lean thinking.
Tools like Easy Agile Scrum Workflow for Jira are available at no cost to ease this positive change. Another tool that complements value stream mapping is Easy Agile Programs for Jira.
Adopting lean principles is much easier with the support of Easy Agile resources, so get your lean team going today.
- Workflow
7 Lean Methodology Benefits for Development Teams
The lean methodology is all about eliminating waste and improving efficiency to maximize and deliver consistent customer value. Under lean, if a process doesn’t bring value to the customer, it’s considered wasteful and is eliminated or reduced as much as possible. It’s a development method and guiding mindset that helps teams refine their processes in the name of efficiency, effectiveness, and continuous improvement.
Here, you’ll learn about the origins of lean as well as 7 key benefits of adopting the lean methodology.
An intro to lean methodology
The lean methodology grew out of lean manufacturing. The concept was introduced in manufacturing to improve profits by reducing costs as opposed to relying solely on increased sales. If a company can eliminate waste and become more efficient, it can save money, which increases overall profits.
While the roots of lean manufacturing can be traced back to the 1400s, Henry Ford first fully integrated the entire production process, creating something called flow production in the form of an assembly line.
This was a revolutionary change in car manufacturing, but while Ford certainly enhanced flow, he didn’t leave much room for variety. In the 1930s and ‘40s, Japanese manufacturers Kiichiro Toyoda, Taiichi Ohno, and others at Toyota made a series of simple innovations that allowed them to provide both continuity in process flow and a wide variety of vehicles, creating the Toyota Production System.
This form of lean production enabled the elimination of waste, reduced costs, increased efficiency, and made information management simpler and more accurate. Lean methodology was further distilled and explored in the books The Machine That Changed the World by James P. Womack, Daniel Roos, and Daniel T. Jones, and Lean Thinking by James P. Womack and Daniel T. Jones.
The latter book also introduced the five key principles of lean:
- Identify Value
- Map the Value Stream
- Create Flow
- Establish a Pull System
- Seek Perfection
Learn more in our article, Understanding Lean Agile and the 5 Lean Principles.
Of course, lean thinking has evolved beyond manufacturing and has been adapted and applied to everything from healthcare to construction to logistics and distribution to government to software development.
1. Increased efficiency ⏳
The application of lean to business processes is all about reducing waste to increase efficiency. But how do you figure out which processes provide value?
Once customer value is identified, teams can create a value stream map. Value stream mapping tracks each of the steps and processes to bring a product from inception to delivery. Organizing your processes visually where everyone can see them allows teams to clearly see what does and doesn’t provide value. If any steps or processes don’t bring value to the customer or are found to be otherwise wasteful, they are eliminated or reduced as much as possible.
A team can’t be efficient if they’re wasting time on tired processes that don’t provide customer value. Adopting lean methods helps to get rid of those processes, so you can dedicate your team’s energy exclusively to the processes that do, thereby increasing your team’s value flow, efficiency, and productivity.
2. Reduced bottlenecks 🛑
A bottleneck or broken process, no matter how small, can totally derail a workflow or make it impossible to meet a deadline.
With lean, tasks aren’t blindly or randomly assigned. Teams work together to ensure work is evenly distributed and deadlines are met. They discuss any potential bottlenecks in advance so they can be solved before they become a financial burden or delay work. Since capacity and WIP (work in progress) items are continually forecasted, monitored, and adjusted with lean, bottlenecks are anticipated in advance, every team member participates, and no one’s time is wasted.
3. Fewer costs (and fewer surprises!) 💸
Eliminating waste means saving money—no matter the industry. Overproduction, having too many materials to store, overhiring, and production bottlenecks are expensive and wasteful. These wastes can be eliminated with better management of processes and systems, enabling companies to always have the right number of employees, amount of materials, and working hours at any given time.
Adopting the lean methodology means increasing efficiency, which benefits any company’s bottom line. Make sure every cost is accounted for and necessary to the production process by consistently reviewing your company’s work processes and eliminating any costs that don’t add value.
4. Systems can adapt better and faster 🌎
Businesses today must adapt faster than ever due to increasing customer demand, rapidly evolving technological advancements, and the COVID-19 pandemic.
The larger the size of the organization, the harder it is to adapt. Long-running business systems were not designed to be flexible, so when adjustments need to be made, it may take months or years before the entire organization is on the same page.
With lean, teams can better adapt. Lean systems aren’t as rigid, so it’s easier to make adjustments along the way, meaning teams will better adjust for unexpected circumstances. The lean methodology can help any business, no matter its size, adapt to changing times gracefully, as lean is the exact opposite of a set it and forget it process.
5. Stakeholder visibility and strong customer relationships 💞
The lean methodology leans into both stakeholder and customer needs, which results in a better end product. Progress in lean is measured based on the value delivered to the customer instead of the completion of tasks.
With lean, customer value is paramount. Every project and task begins with considering the point of view of customers and putting yourself in their shoes. Feedback is gathered alongside product development instead of at the end to ensure new information is considered and that the final product will be exactly what the customer needs or wants.
6. Continuous improvement mindset 🧠
Lean is the enemy of the status quo. Lean demands the constant fine-tuning and refinement of processes and enables a continuous improvement mindset. It’s not a “set it and forget it” process, as lean is all about consistent process improvement. No matter how successful or efficient the company is, there is always room for improvement and new, innovative ways to bring value to the customer.
This attitude instills a continuous improvement mindset in everyone involved on the team, whether it’s a small development team or an entire lean enterprise (SAFe). Teams can anticipate and expect regular feedback from leaders, managers, and stakeholders. With lean, innovations and iterations are less precious and more plentiful. The team continues to improve and fine-tune their skills and processes with each passing product.
7. Increased team engagement 🤝
Employee disengagement is expensive. Disengaged employees have higher absenteeism, lower productivity, and lower profitability — all of which can majorly drain a company’s resources. If a company’s culture doesn’t inspire employees to show up and do their best, that company is going to hemorrhage money every year until its bottom line bottoms out.
A lean organization, on the other hand, puts teams on the frontline of product development. Under lean management, employees have direct and regular contact with managers about how their work is going and how the process could be improved. Since teams are more involved in the process, they are more engaged and more likely to actively participate, provide feedback, and buy into their work.
Engaged employees are a company’s greatest asset. Bringing everyone into the process gives teams ownership over the outcomes, boosting their creativity as well as their accountability. Increased team engagement means enhanced efficiency, effectiveness, and team morale.
You can apply the lean methodology anywhere to reduce waste and improve efficiency. Let’s recap. The top benefits of adopting lean include:
1. Increased efficiency
2. Reduced bottlenecks
3. Fewer costs (and fewer surprises!)
4. Better and faster systemic adaptation
5. Stakeholder visibility and strong customer relationships
6. Continuous improvement mindset
7. Increased team engagement
Agile made easy
Easy Agile can help your agile team work better together to deliver for your customers. We have a suite of agile apps for Jira designed to put the customer first through every step of the product development process. From team agility with Easy Agile TeamRhythm, to scaled agility with Easy Agile Programs, our plugins work with multiple agile frameworks, including Kanban and Scrum.
If you work with Jira, you’ll find our lean tools especially helpful for improving the functionality of your workflows and enhancing team collaboration.